Roger Solsona Gómez
Los ortopedas eran considerados maestros artesanos que con destreza manipulaban y daban forma a materias nobles como la piel, acero, madera, etc. Con la aplicación de sistemas informáticos e impresoras 3D, podemos afirmar que la ortopedia ha descubierto su faceta más científica, ya que ahora podemos cuantificar y valorar los niveles de descarga, presión, rotación, alineación… que aplicamos en nuestros dispositivos ortopédicos.
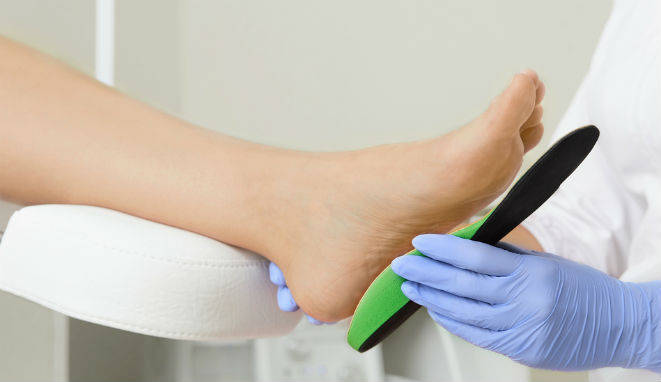
Desde el inicio de los tiempos, la ortopedia se ha caracterizado por ser un trabajo artesanal. Los ortopedas eran considerados maestros artesanos que con destreza manipulaban y daban forma a materias nobles como la piel, acero, madera, etc.
En el imaginario colectivo permanece la imagen de un pirata patapalo, que refleja cómo fueron los inicios de esta disciplina.
Con la llegada de los plásticos, y más concretamente el termoplástico, la ortopedia sufrió un cambio a nivel cualitativo y cuantitativo: se producían más aparatos y con menos costes económicos, pero continuaban requiriendo de la destreza del artesano a la hora de rectificar los moldes positivos.
Hoy en día, se está haciendo especial énfasis en la aplicación de los sistemas informáticos en el campo de la ortopedia, que desde la aparición de los termoplásticos se considera unos de los principales avances en el sector desde hace años.
La faceta más científica
Con la aplicación de estos sistemas informáticos e impresoras 3D, podemos afirmar que la ortopedia ha descubierto su faceta más científica, ya que ahora podemos cuantificar y valorar los niveles de descarga, presión, rotación, alineación… que aplicamos en nuestros dispositivos ortopédicos.
En el campo de las ortesis plantares, podemos empezar nuestra visita al paciente con la ayuda de una plataforma baropodométrica para realizar un estudio de la pisada o más conocido como estudio de la marcha.
Estos instrumentos suelen ser unas plataformas o cintas de marcha con miles de sensores que nos darán información de la posición del pie, presiones, morfología, líneas de carga… tanto en estática como en dinámica.
Esta información nos será útil, junto con la prescripción del facultativo que nos deriva al paciente, para poder complementar la anamnesis (o historia clínica) de nuestro cliente y elegir así los materiales más adecuados para poder fabricar la ortesis plantar en función de su edad, actividad, patología, etc.
La importancia del molde
Para realizar estas plantillas, deberemos obtener un molde del paciente para poder fabricarlas, hasta ahora, sólo contábamos con técnicas como la espuma fenólica o los moldes de escayola o resina.
Con los escáneres 3D tenemos una información más precisa
Con la aparición de los escáneres 3D, tenemos una información más precisa, ya que el margen de error en la medición de estos instrumentos ha disminuido considerablemente en los últimos años, haciendo que este error sea prácticamente inexistente. Además, este método es más rápido y limpio que los sistemas convencionales.
Una vez hemos obtenido nuestro molde positivo, es decir, una copia exacta del pie de nuestro paciente, es el momento de realizar la fabricación de la plantilla. Empezamos por el diseño o maquetado de la ortesis plantar, por medio de un programa informático basado en la tecnología cad-cam.
Empresas como Biomech Consulting, se han especializado en el desarrollo y servicio de este tipo de programas, ofreciendo a sus clientes la posibilidad de subcontratar el diseño y fabricación de ortesis plantares de un modo rápido y sencillo.
Valores numéricos
Con el diseño de la ortesis plantar, podremos observar los valores numéricos de la rectificación de esta plantilla y cuantificar la descarga que se le va a aplicar a este pie.
A diferencia de los sistemas tradicionales que dependían de la destreza del artesano, hoy en día, tenemos la posibilidad de cuantificar y corregir a través del sistema informático antes de pasar al proceso de fabricación.
En último lugar, la información obtenida en el programa de diseño se reenvía a una máquina de fresado, donde después de elegir el material que se utilizará de base en la plantilla se procede al proceso de fabricación de esta.
La máquina de fresado trabaja con unas brocas de precisión que rebajan bloques de material especifico como pueden ser EVA, polipropileno, o materiales compuestos como la fibra de carbono.
El fresado nos permite tener la ortesis en un menor tiempo y con una precisión más correcta
La ventaja del fresado es la de trabajar el material a temperatura ambiente con lo que no se alteran las propiedades moleculares de dicho material, como ocurre en el termo moldeado, con lo que desaparece la deformación de la ortesis por una mala reestructuración molecular durante el proceso de fraguado del material.
Esto nos permite tener la ortesis en un menor tiempo y con una precisión más correcta.
Cuando se ha obtenido el fresado de la plantilla, sólo necesitaremos acabar la ortesis aplicando las descargas pertinentes que no se hayan podido fresar y forrando la superficie que irá en contacto con el pie del paciente para mejorar su comodidad.
Roger Solsona Gómez es profesor adjunto del Curso de Ortopedia para Farmacéuticos online.